Misc.
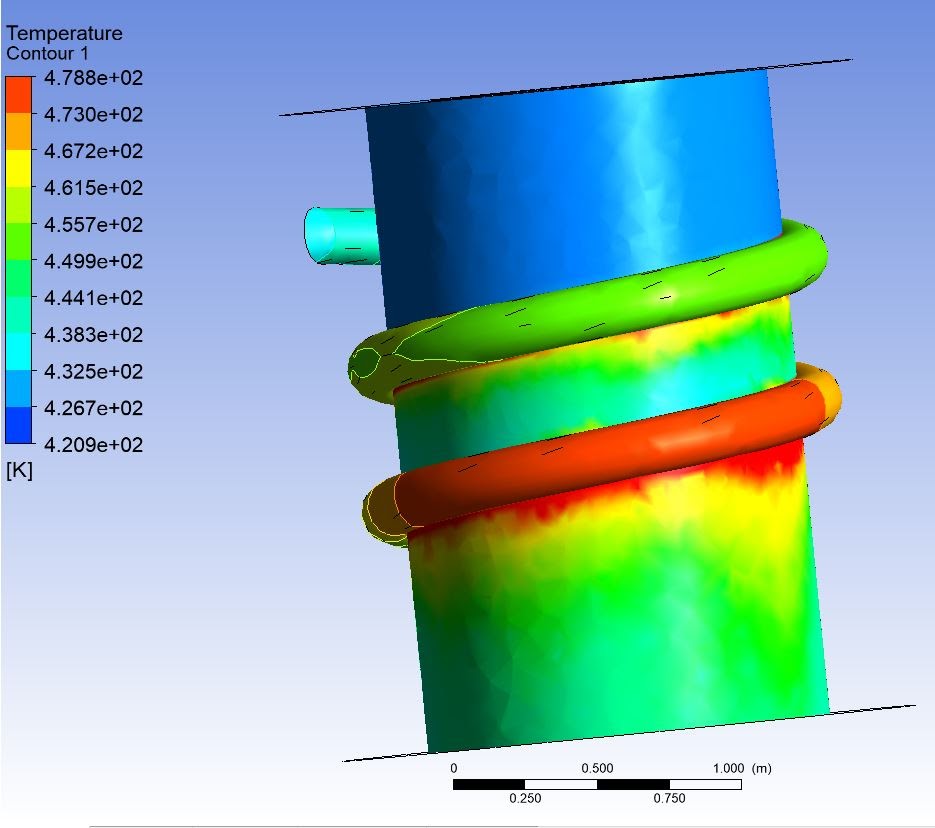
A problem with space travel, particularly relevant now due to talks of long duration missions to mars and beyond, is water storage. During my Computational Flow Dynamics course in the Spring of 2019, I worked with a group on a heat transfer project. Our project examined efficient water recycling in space suits. By circulating exhaled air through a cooled pipe the water vapor in the air would condense out. By collecting this condensed water, clean water could be recycled and would reduce the need to take large water reserves into space.
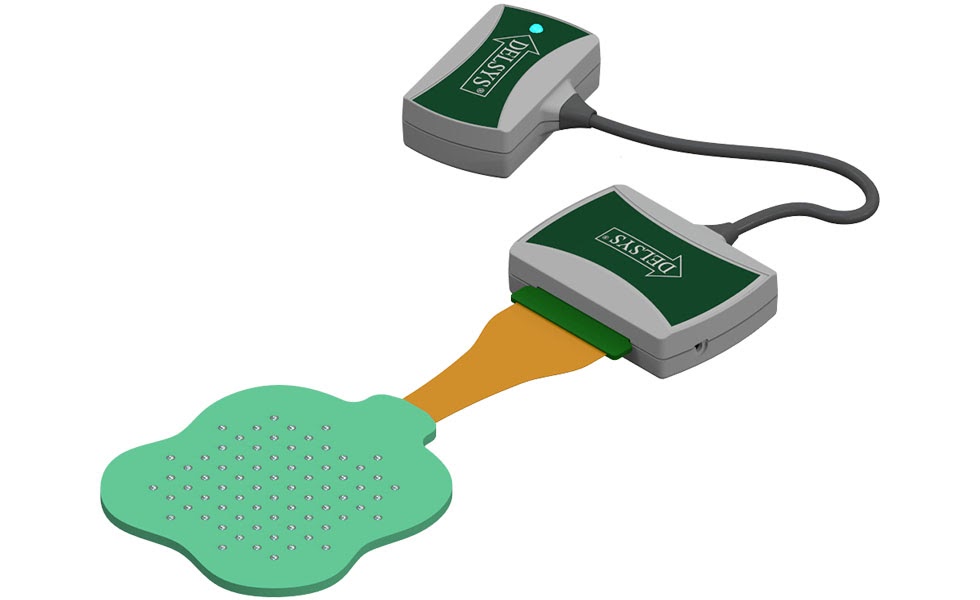
During the Fall of 2019 I connected with, and assisted, a professor who had been doing research regarding EMG (electromyography) for use in prosthetics. This research aimed to facilitate the use of prosthetics by improving the ease of use between the human user and the artificial sensor. This technique involves placing an array of sensors above the muscle, detecting irregularities, and selecting the cleanest signal from the array. This method, if implemented, will allow for easier and more accurate signal collection for active prosthetics. Programming work and machine learning for this project were undertaken with the aid of MATLAB.
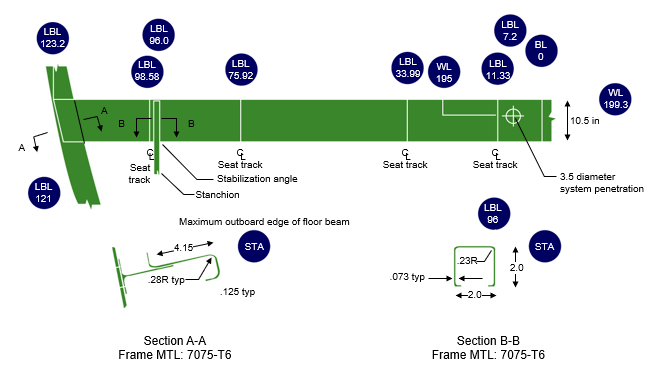
This is a project that I worked on during the Spring semester of 2019. It was under the direction of John Keil, an Engineering Senior Manager from Boeing. We were tasked with designing a floor beam for the fuselage of a 747, as well as meeting the pertinent FAA requirements. We were given the design loads, attachment points, and a bounding box to design within. My group used Excel, MATLAB, some initial guesses, and lots of iterating to come to a final design. We took into consideration the material of the beam, the type of corrosion resistant coating applied, the method of manufacturing, and bolt patterns through the use of trade studies. Our group was highly praised by Keil and the course instructor for our use of GRANTA Selector (known as CES at the time) to select the best possible material. The material, along with an efficient geometry led to reduced weight, minimal machining time, and finished with us designing the lightest and cheapest beam. The beam was modeled within SolidWorks.